digital document processes
d.velop products for digitalisation in the mechanical engineering industry
Digital transformation is opening up new opportunities for mechanical and industrial engineering. At the heart of this is the networking of people and machines. Increasing amounts of data must be available very quickly, and the entire production chain must be more agile than ever. The d.velop platform and the associated product range support you in handling digital document processes – including the special requirements of mechanical engineering. From the digitised machine dossier to the digitally documented ordering process and the product dossier – all document-based processes can be implemented.
Manage and archive documents quickly and easily
With d.velop documents you accelerate, simplify and optimize the management of your documents.
- Seamless integration: No more constant switching between specialist applications
- Efficient administration: Access, display and store documents and files in seconds
- Legally compliant archiving: Based on the GoBD
- Smart processes: Workflows and automatic archiving of the workflow log
Expand your system and centralize all your documents using digital files. Have all information in one place and access your digital archive across locations.
With d.velop process studio, you can relieve your employees of time-consuming routine tasks and accelerate the flow of information in your organization – quite simply with workflow management.
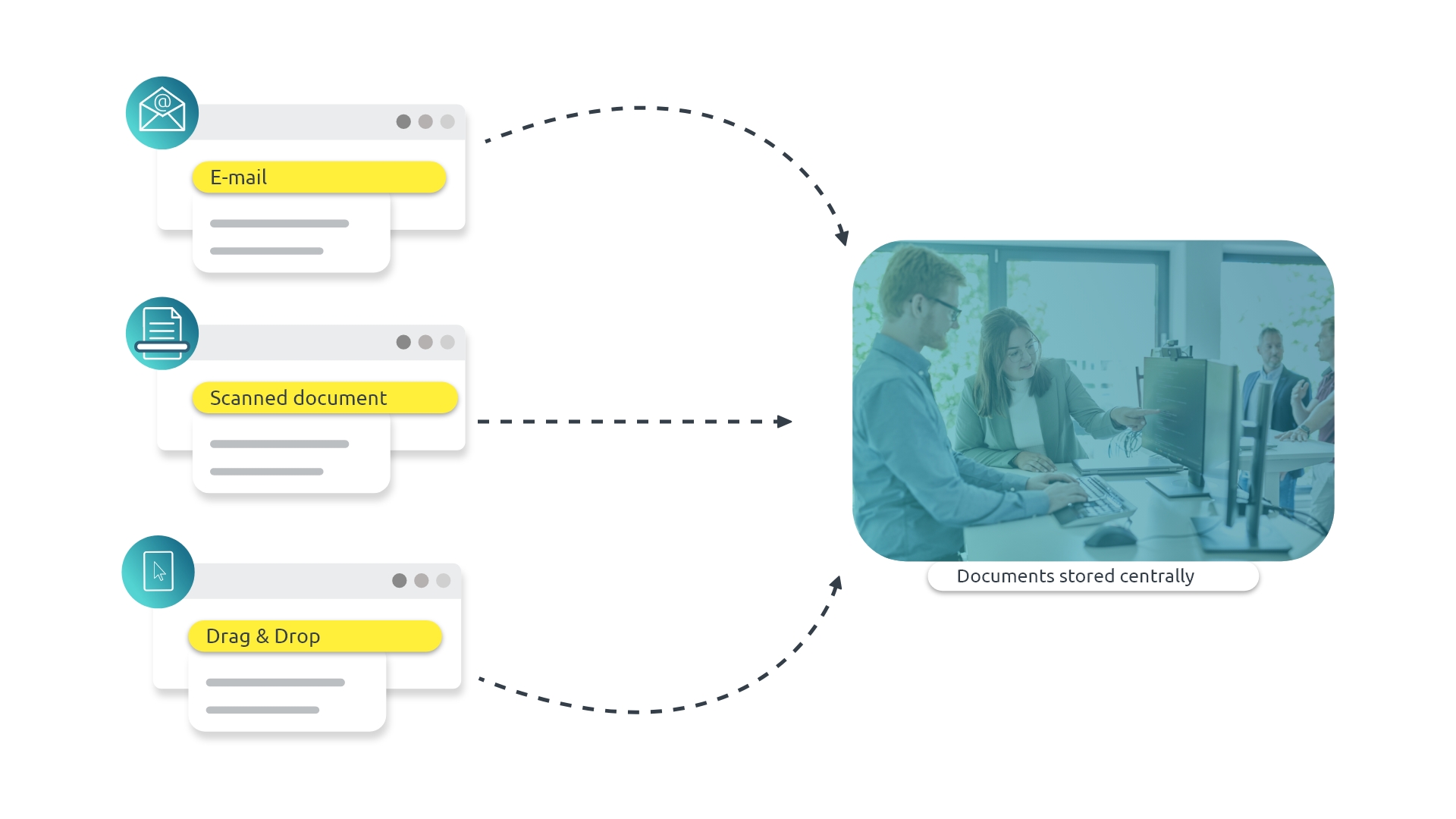
Manage invoices digitally and automatically
With the help of our digital invoice processing, you can streamline and simplify your processes. It starts with scanning the invoices. Followed by the automated reading of header and item data, through to approval and posting in the system.
- Automated recording of invoices: Whether paper, e-mail, XRechnung or ZUGFeRD
- Factual check and approval: With or without order reference and with complete logging
- Integrated workflow: Individual customization and authorization options
- Cross-location checking: Checking via smartphone possible
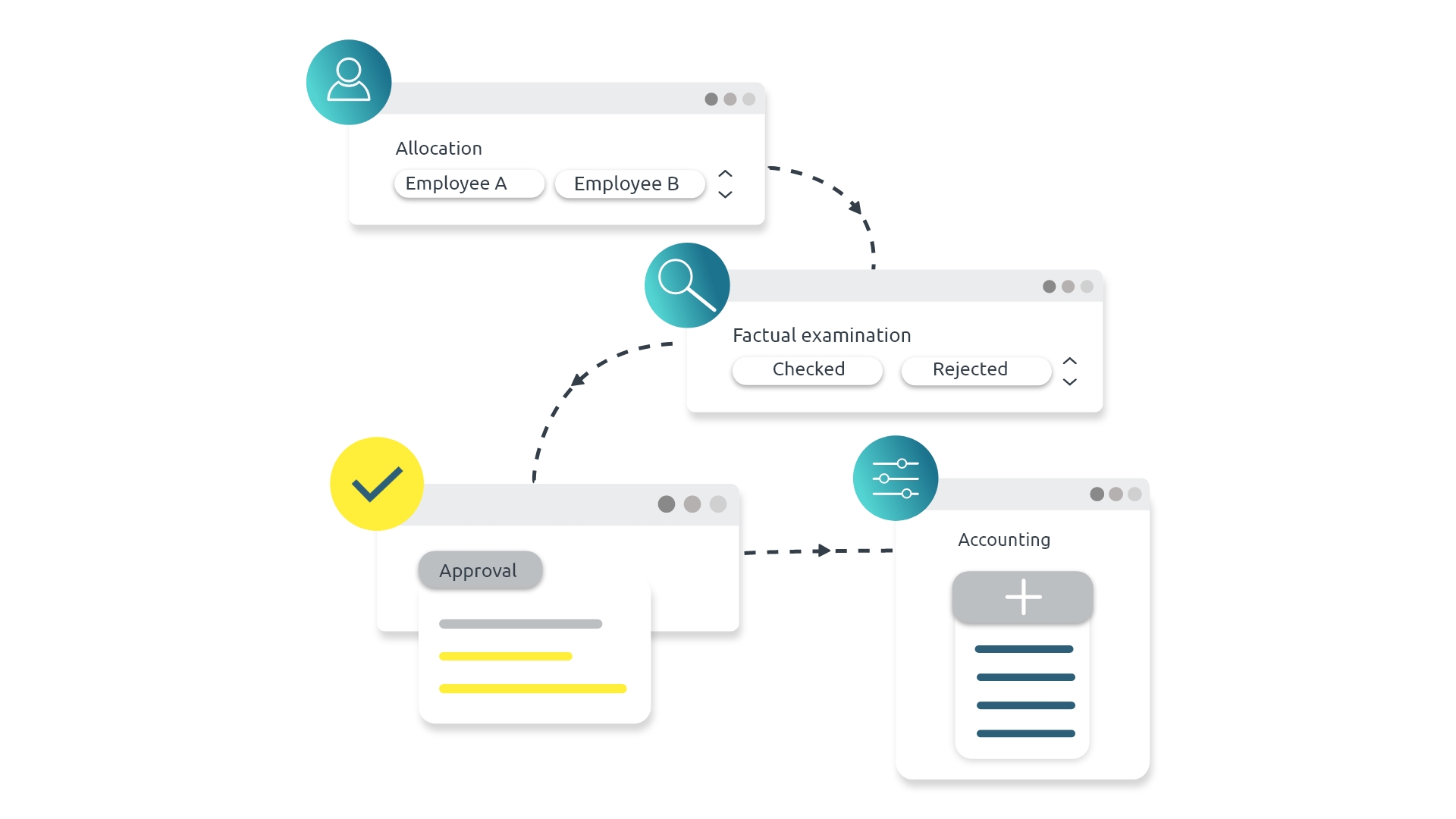
Manage contracts successfully
Contract management is a time-consuming and sometimes laborious task. In many companies, it is unclear how contractual obligations are managed, evaluated and actively used for corporate and organizational management. Employees from almost all departments have points of contact with contracts. Digital contract management offers many advantages here:
- Transparency: All contracts at a glance and no more missed deadlines.
- Efficiency: Faster creation, processing and evaluation of contracts.
- Security: No more lost contracts and cross-departmental working.
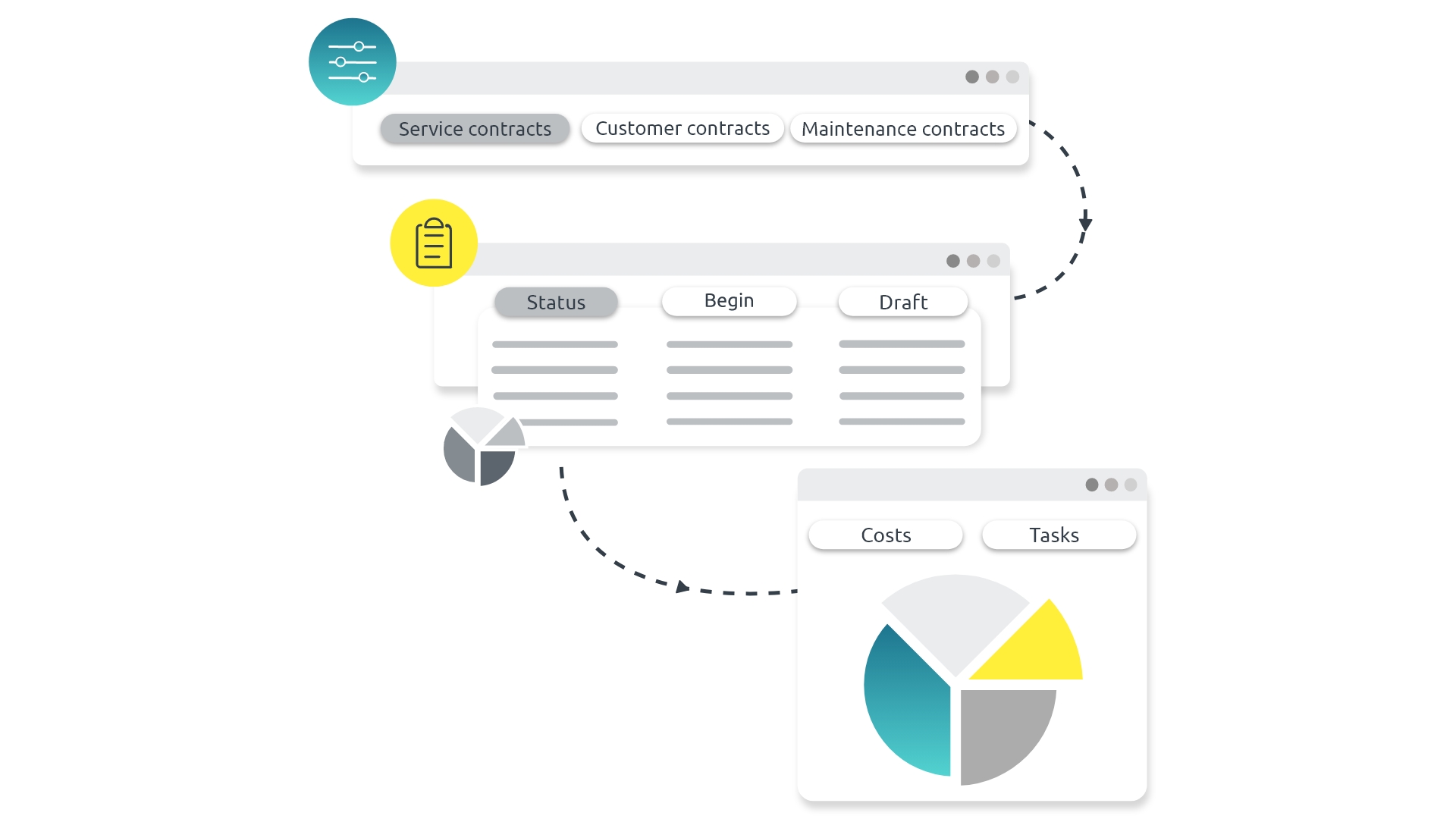
Legally secure and digitally sign documents
Endless stacks of paper, time-consuming processes, inadequate data protection? Many companies are confronted with these challenges on a daily basis. d.velop sign is a German eSignature that helps people from all sectors to completely digitize the signature process. No hardware or software installation is required to use it, as d.velop sign is completely cloud-based.
- Save time: no need to go to the printer, no long waiting times
- Reduce costs: save paper, printing and shipping costs
- Location-independent: Sign documents regardless of location
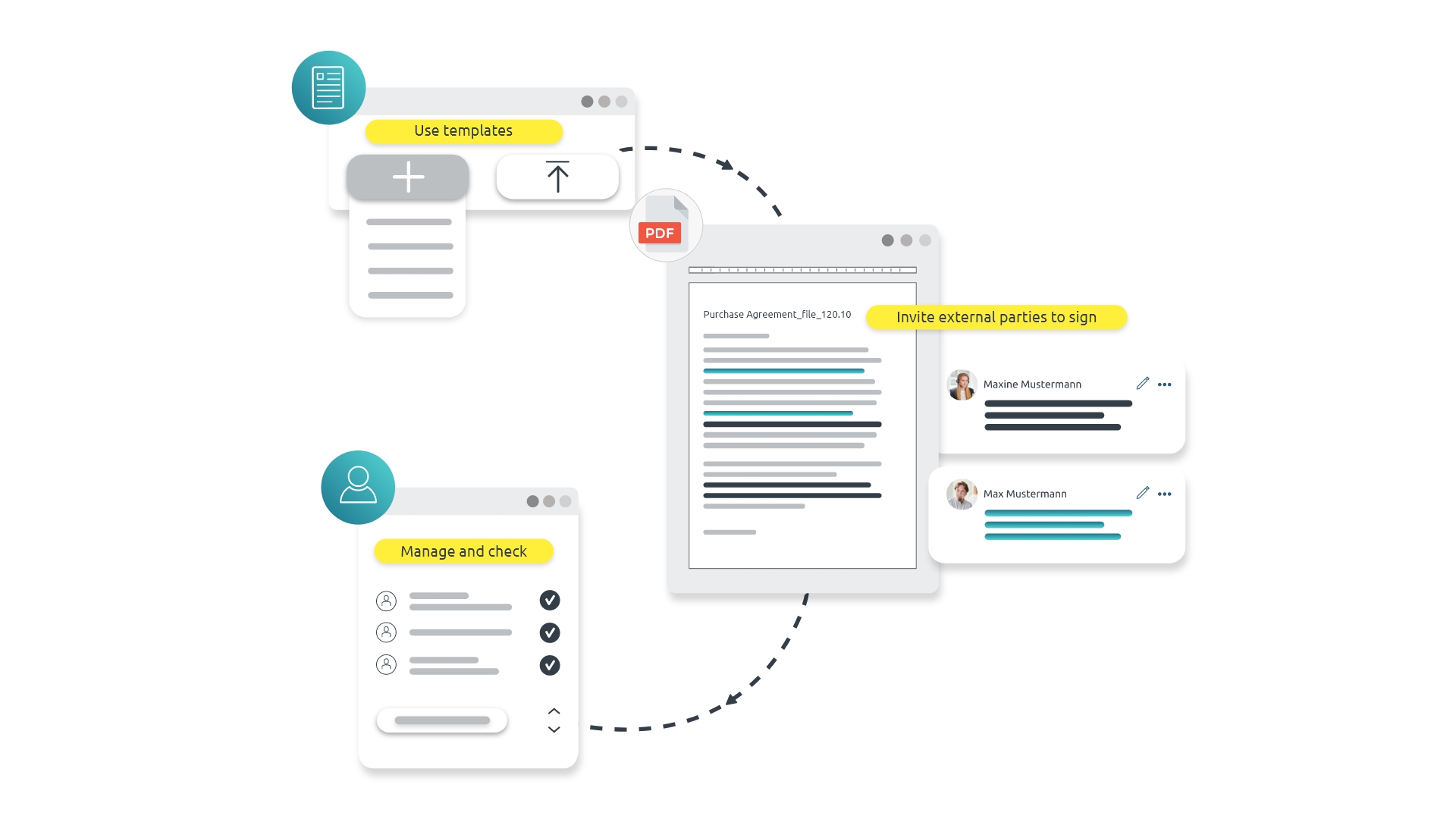
Automate personnel processes
The digital personnel file from d.velop digitizes and automates your personnel processes and ensures greater transparency. To this end, the file manages all personnel documents – from application documents to contracts and payslips to sick notes – and accelerates the handling of HR processes.
With d.velop postbox, you can provide employees with documents such as payslips and social security documents in a cost-efficient and compliant manner. Delivery is encrypted.
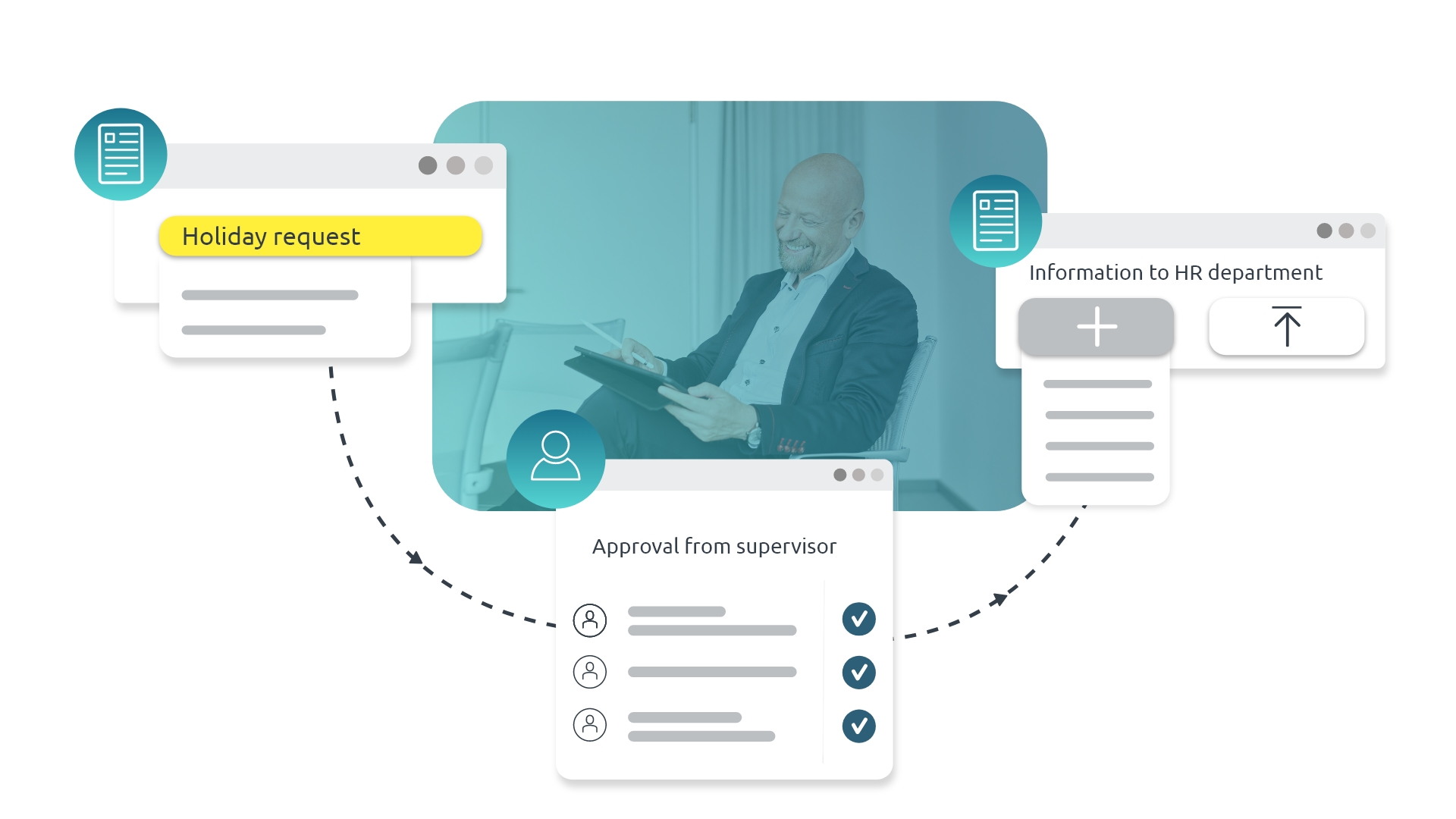
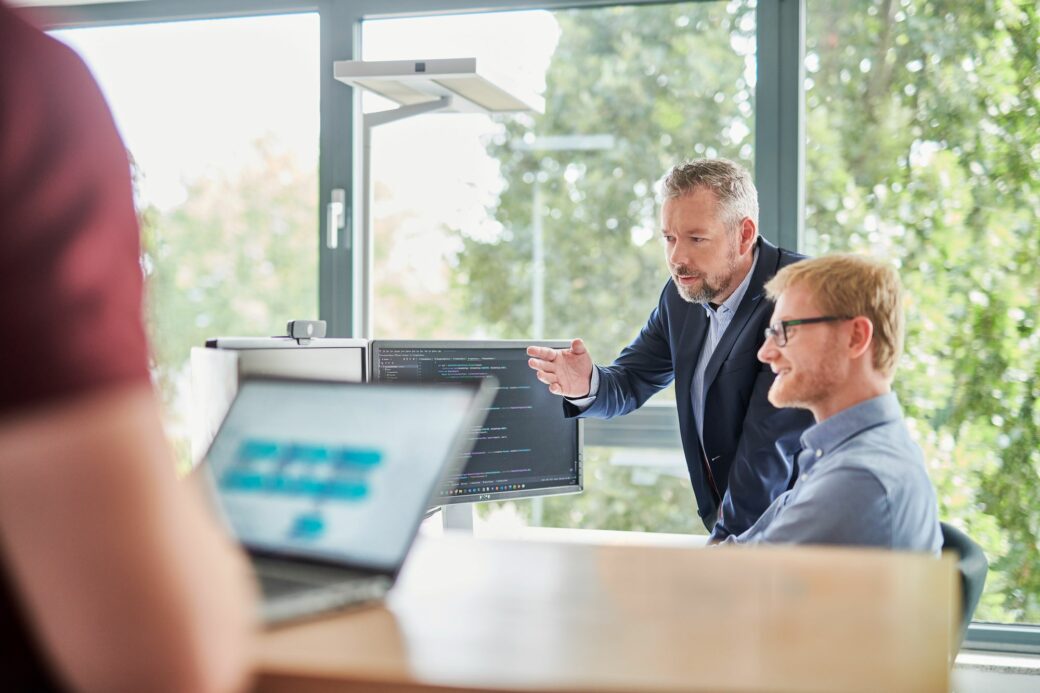
Webinar
Make your invoice process an enjoyable, digital experience
Invoice processing is a great example. Manual invoice processing drains you of valuable resources like energy, time, money and the ability to focus on more meaningful work. Yet the whole process can be seamlessly digitalized. Let the machines do the heavy lifting for you! Watch our Smart Invoice Processing webinar and learn how to automatize your invoice workflow.
Use Cases
Use cases of d.velop software in the mechanical engineering industry
With the software solutions of the d.velop platform, you can digitalize your mechanical engineering company holistically. Benefit from over 25 years of experience, which we incorporate into our projects and specialist solutions. Take a look at selected use cases from the mechanical engineering sector in detail.
TEST Software NOW
Get to know d.velop software
Request a personal live demo of d.velop software in just a few clicks. Let us show you the software live and you can ask your questions directly. Just complete the form and we’ll get in touch.