The fabric behind the management of 9 million documents
What does fabric actually sound like? And how can a motorcycle suit offer maximum protection while remaining comfortable and breathable? Schoeller Textil AG provides answers to such questions with textiles that are in demand around the globe. When it came to answering their own questions about document management, they turned to adeon ag – and the d.velop DMS.
Schoeller Textil AG
Schoeller Textil AG celebrated its 150th anniversary in 2018. The company, which is based in Sevelen in the St. Gallen Rhine Valley, produces special fabrics for products such as riding pants, police uniforms, backpacks, outdoor gear and motorcycle clothing. They even make the fabric sheathing for mobile Bluetooth speakers. Ruedi Kühne, Chief Financial Officer of Schoeller, explains: “When a world market leader first asked us for such a fabric, we were faced with an unknown challenge: How does our fabric actually sound? We found the solution by modifying an abrasion-resistant and waterproof fabric originally designed for motorcycle textiles.”
Schoeller produces fabrics in three stages with 200 employees. In the first stage, the fabric is woven from yarns. Next it is dyed, and then in the third stage it is finished. One example of such finishing is sandwich constructions for functional textiles: A membrane system on the inside is combined with layers of fabric on both sides. The textiles, 90 percent of which are used outdoors, are then delivered on rolls to customers all over the world.
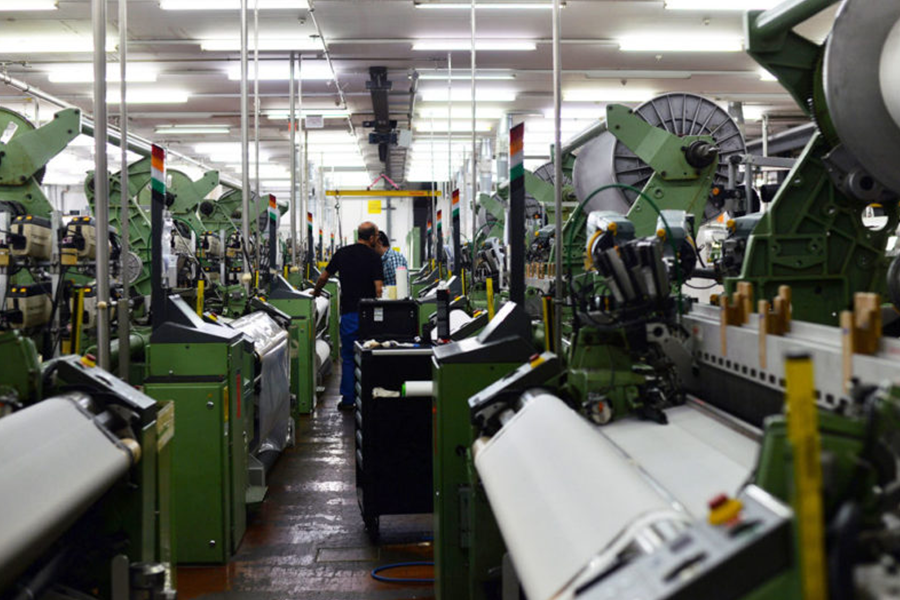
Email Archiving
Product
200
Employees
Consumer Goods
Industry
An electronic archive since the beginning of the 2000s
As early as the 2000s, Schoeller began building an electronic document archive for its financial accounting in Sage 200, as well as for its production and planning software TIM. The archive for financial accounting, including all financial records, was implemented back then by adeon using Comarch DMS Infostore. In 2007, email archiving was added. But a new challenge soon emerged, as Ruedi Kühne explains: “Two years ago, we received the first indications that Infostore would no longer be developed. So it was time to look for a new solution. We asked adeon, our trusted implementation partner, and another provider to present possible options.” Adeon’s solution: the powerful and future-ready document management system from d.velop. “It’s now much easier to assign documents to an order. Everything is clearly logged, and you can see exactly what was done and when,” says Kühne.
Everything that had previously been archived electronically was to be transferred seamlessly into the new archive.
Schoeller’s requirement: all existing electronically archived content had to be fully migrated and made accessible in the new system. “We’re talking about seven million emails and one million other documents that we wanted to access at any time,” says Ruedi Kühne. At the same time, the scope of document management was to be expanded to include additional areas: ISO certification, the supplier complaint process, and customs clearance.
Converting the entire accounting archive
adeon’s offer won them over. “The solution met our requirements. In addition, we have worked with adeon for over 15 years. We know their people, and their people know our systems. There is no need for much explanation or communication. We were able to get started with the project right away.” Converting the accounting archive was the simple part. The task was to make all electronically stored data available via d.3ecm. Adrian Dähler, the project manager at adeon, explains: “Our expertise allows us to integrate very deeply into other systems. At Schoeller, we integrated d.3ecm seamlessly into the leading systems TIM and Sage 200. This means that all search queries can be covered by both systems.” According to Dähler, “the implementation of d.3ecm makes it possible to call up documents from accounts payable and accounts receivable going back decades based on any conceivable search criteria.”
An archive of seven million e-mails
A major challenge was transferring the archive and its seven million e-mails from Infostore to the d.3 server. Adrian Dähler explains: “We had to safely transfer this enormous amount of data to d.3ecm so that all documents would remain accessible and the mail server would be unburdened of past correspondence.” Dähler adds: “Nothing can be forgotten anymore because the process automatically reminds you to process e-mails.”
Despite the new system, you can still access any archived e-mail at any time. “At the push of a button,” confirms Ruedi Kühne, who is impressed with this ability to scour the entirety of the company’s business correspondence. About once a week he has to go back to older e-mails. The system automatically notices when this is the case.
“A document management system is a no-brainer.”
Ruedi Kühne
CFO
Schoeller Textil AG
A new scheduling and planning process for added convenience
Further tasks were added. One of them was particularly sensitive: the scheduling and planning process had to be switched over for the big day. “And it worked smoothly,” says Ruedi Kühne appreciatively. The workflow engine looks at other systems and notices when a new customer order is opened in ERP. It then instructs the scheduler to confirm the delivery date within the next few days. The system checks when production and delivery are possible and shows when the order confirmation can be sent. In short, the scheduling and planning engine reminds you of every workflow and can even escalate to the superior if something is not done on time. Because the reminder function greatly relieves employees and streamlines work processes, it is also very valuable for Schoeller’s ISO certification.
The workflows are now clean and elegant. “It is now much easier to assign documents to an order, set links, confirm tasks. In addition, everything is neatly logged, so you can see exactly what was done and when,” says Ruedi Kühne.
It’s now much easier to assign documents to an order, create links, and acknowledge tasks. Everything is clearly logged – you can see exactly what was done and when.
Ruedi Kühne
CFO
Schoeller Textil AG
Paper documents are no longer needed
Schoeller no longer keeps paper in many departments. Whether it’s accounts payable or receivable documents, supplier or production papers or customer dossiers, everything is now stored in a structured manner and can be retrieved at will using search queries. Ruedi Kühne appreciates the flexibility offered by d.3ecm: “The interfaces are uniform, but each user can access a document in his or her preferred manner. This is one of the great advantages of the electronic archive: I can search in many ways—by name, date or order number—and nobody can remove or misfile the original anymore. It always stays right where it belongs.”
As soon as a case is entered in the accounting system, a document receives a bar code that can be stuck on any paper document that is still required for the case. The accounting department then need only scan supplier invoices, accounts receivable documents and production slips—batch by batch—and each document is automatically assigned to the corresponding order via the codes.
Supplier complaint process saves cash
Ruedi Kühne particularly likes the supplier complaint process set up by adeon. This enables Schoeller to process complaints against suppliers. Schoeller has around 700 suppliers—200 for raw materials alone. Here, every mistake means cash.
“Now nothing can be forgotten when a supplier delivers bad material because the process automatically reminds you to process the case.” Schoeller continues to optimize its processes. adeon is currently implementing interfaces for EasyExport, a software for declaring goods to customs. This means that customs documents can also be filed out in d.3ecm. Another benefit for employees is that they can immediately see which customs order belongs to which supplier.
A purely electronic quality management system
Ruedi Kühne is also responsible for quality management, which Schoeller is currently implementing. Naturally he wants to do away with paper here too. Schoeller delivers a lot to the public sector: to the Belgian and the Hong Kong police, the post office, SBB and other organizations. “We were under increasing pressure to get certified according to ISO 9001.” The certification process has now begun. The documents are stored electronically, from visitor reports to process descriptions. One major advantage is that only the current reports that are actually needed are displayed. d.3ecm tells you which version was created and signed by whom and when. Processing is easily traceable, which considerably simplifies quality management. “We recommend adeon without reservation,” says Kühne.
Authorization management is a core element of the new d.3ecm solutions for Schoeller. It can be used to define who has which authorizations to view or edit documents. In addition, log files show which person viewed or edited a document and at which time.
Schoeller Textil AG is happy with the new system. It knows it can count on a modern platform from well-known manufacturer d.velop and expert maintenance—and on the fact that the system will still exist in ten years. Another significant advantage of the new solution is that authorized employees can access documents remotely at any time—just as if they were at their workplace. “We have been working with adeon for almost 18 years now. We can fully recommend the company,” concludes Ruedi Kühne. So it’s not just the fabric on your speakers that sounds good to your ears; it’s adeon’s new solutions, too.
Project partner
adeon ag is a committed team of highly-qualified and experienced specialists who develop and implement innovative solutions in the fields of document management, electronic archiving and workflow (Business Process Management, BPM). Sustainable process optimizations need a competent partner. The adeon ag team applies its knowledge and many years of experience in a systematic way to closely analyze problems, define in-depth concepts and precisely coordinate their implementation. adeon ag is the competence center for ECM solutions for d.velop and, in its role as managing distributor, is responsible for the markets of Switzerland and the Principality of Liechtenstein.
Software Demo
Learn more about the d.velop software
Request your personalised live demo of the d.velop software with just a few clicks. Get a live demonstration of the software and ask your questions directly. Simply fill in the form and we will get back to you.