GREIWING – A Specialist in Logistics Services
What do the chemical, food, plastics, and hazardous materials industries have in common? A logistics expert: GREIWING logistics for you GmbH, based in Greven, North Rhine-Westphalia, specialises in providing logistics services for these sectors.
Founded in 1930, GREIWING has grown into an internationally recognised specialist in what is known as silo logistics. This involves all goods stored in silos – such as plastics, construction materials, granulates, or foodstuffs – that are free-flowing.
With over 1,000 employees at 18 locations across Germany and one in Belgium, GREIWING generates annual revenues of more than 130 million euros. But GREIWING offers more than just transport from A to B. As a logistics service provider, the company often becomes deeply involved in its clients’ value chains – for example, in sorting, homogenising, or drying granulates.
Moving Away from Isolated Solutions – Towards Integrated Processes
To reliably and securely integrate into a client’s value chain, expertise and experience are essential. Isolated solutions are of little help in such demanding projects. Skilled logistics professionals combine knowledge from various industries, professions, and projects to deliver the ideal solution for each case.
Ideally, an IT infrastructure supports this approach. After all, siloed knowledge is virtually worthless – value is only created through accessibility and interconnection, much like in silo logistics itself.
d.velop documents & invoices
Product
1000
Employees
Logistics
Industry
Knowledge Must Remain Usable
In 2010, GREIWING realised that its IT landscape no longer fully met its own standards. Although the logistics company was already working with a digital document management system, “our archives were divided into several areas that couldn’t be linked together,” recalls Marcus Oberfeld, Head of IT and Organisation.
Paper Files Slowed Down Workflows
Other traditional processes were also being challenged by new technological possibilities. One example: paper-based project files. “We used to archive all information – such as correspondence and receipts – in numerous folders from various departments. Colleagues often had to search for the right folder.” In some cases, entire review processes had to be repeated from the beginning because the last reviewer in the chain had found an error. Instead of simply correcting the mistake and moving on, the whole process had to start over.
Oberfeld explains: “At some point, our finance department simply stopped handing out folders to avoid having to search for them later. Anyone who needed a copy had to make it on site. Today, things are much easier – we can even access documents on the go using a smartphone or tablet.”
An Alternative to the Existing Document Management System
At the same time, GREIWING was transitioning many of its IT systems to SAP ERP, and an update to the existing document management system was due. “But the previous provider seemed intent on selling us the update at the highest possible price,” says Marcus Oberfeld. So in 2010, GREIWING began looking for alternatives.
One such alternative was found close to home in North Rhine-Westphalia: the d.3ecm document management system from d.velop AG. It didn’t take long for GREIWING to choose d.3ecm. One of the key reasons, according to Oberfeld: “With d.velop, costs are transparent and predictable – we know what to expect in advance. There are no thresholds where licence costs suddenly spike once a certain number of documents is reached. On the contrary, costs grow in line with usage.”
Freight Documents – Securely and Quickly Archived
A prime example of the system in action is the archiving of freight documents. Everything GREIWING prints, everything returned by customers, and everything drivers carry with them is automatically stored in the electronic archive. Drivers scan the documents directly in their trucks or use barcodes that are scanned along with the documents. So far, so good – and not always standard practice. The real advantage: if an employee needs to look up a case, they no longer have to click through endless Windows folders or navigate different departmental filing systems.
d.velop Offers Deep Industry Expertise and Cloud Know-How
Over the years, GREIWING continued to grow – gaining new clients, employees, and services. Naturally, the IT infrastructure had to keep pace. “In recent years, we’ve experienced very dynamic growth,” recalls Marcus Oberfeld. “Our own servers could no longer keep up.”
What to do? Expand the IT landscape? That would not only mean more work for IT staff in the short term, but also more time spent in the future on maintenance, updates, repairs, and expansions. GREIWING didn’t see that as a sustainable path. Oberfeld explains: “We wanted to focus more and more on specialised IT tasks related to logistics. Anyone can maintain servers, but we have company-specific knowledge that we want to put to use. That’s why we’ve been undergoing a transformation process since the late 2010s.”
Less Hardware, More Cloud Services
The goal: to reduce reliance on in-house hardware and increasingly adopt cloud services. For this, GREIWING once again turned to d.velop AG as a partner – and for good reason, says Oberfeld: “d.velop has deep industry knowledge. They understand what a logistics company is trying to achieve when it wants to archive certain documents – customs forms, CMRs, and other records. We didn’t have to explain that to them. They could anticipate our needs and understood the logistics context.”
“In recent years, we’ve experienced very dynamic growth, and our own servers could no longer keep up. We wanted to focus more on specialised IT tasks in the logistics sector. Moving to the cloud has freed up working time. And thanks to digital invoice processing, we can now see immediately when documents haven’t been approved. As a result, our cash discount earnings have increased significantly.”
Naturally, Moving to the Cloud Raises Questions
- Are the internet bandwidths sufficient?
- How responsive is the cloud storage? In other words: can employees work at their usual speed, or do latency issues cause delays?
- How are existing data transferred to the cloud? And how long does the migration take?
- How can a company ensure it chooses the right cloud provider?
Tests Confirmed: Faster Workflows with the d.velop Cloud
“The availability of sufficient bandwidth is, of course, what makes such a project possible in the first place,” explains Stephan Feige, Market Director Logistics at d.velop AG. “And initially, GREIWING didn’t know how high-performing the d.velop cloud solution would actually be. There were concerns about whether documents would display as quickly as employees were used to. In a test, we were able to demonstrate just how fast it is – and GREIWING was very impressed. The response time is just as fast as with the previous system.”
Marcus Oberfeld adds: “For us as users, nothing really changed – we tested it with a stopwatch. Today, the necessary bandwidth is simply available. In principle, we did exactly what we always tell our customers: don’t hire extra drivers, don’t buy trucks – let the specialists handle it.”
For the transfer of existing data – the migration – GREIWING chose a tailored approach. The company defined a cut-off date in 2019, from which all new data would no longer be written to the old system but directly to the cloud. “In the end, we were also running out of storage space,” says Oberfeld.
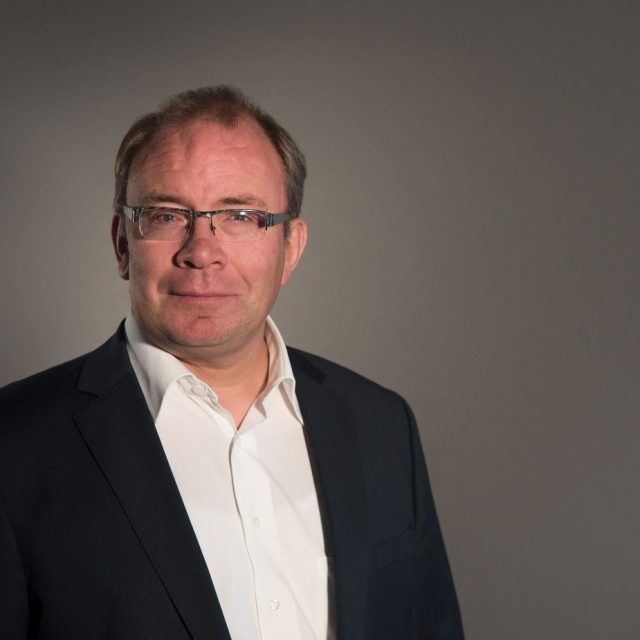
d.velop has extensive industry expertise. They understand exactly what a logistics company needs when it comes to document archiving – customs documents, CMRs, or other records. We didn’t have to explain it to them – they were proactive and already familiar with the logistics context.
Marcus Oberfeld
Head of IT and Organisation
GREIWING logistics for you GmbH
Migration of Over 10 Terabytes of Data Took Three Months
Naturally, the existing data still had to be transferred to the cloud. To do this, GREIWING booked specific time slots with its internet provider – after business hours and on weekends – with increased data transfer rates. In total, more than 10 terabytes of data were transferred in the background, a process that took around three months.
Even During the Transition Phase, the Benefits of the Cloud System Became Clear:
- Secure backup procedures included
- Data stored with high availability, redundancy, and fail-safety in a data centre in Frankfurt
- No need for GREIWING to maintain, service, or regularly update its own IT infrastructure
- IT resources freed up for logistics-specific projects
- Reduced urgency to recruit new IT specialists
- Cloud solution proved more cost-effective than an initial investment in equivalent hardware
- Cloud systems are protected against accidents and disasters such as flooding
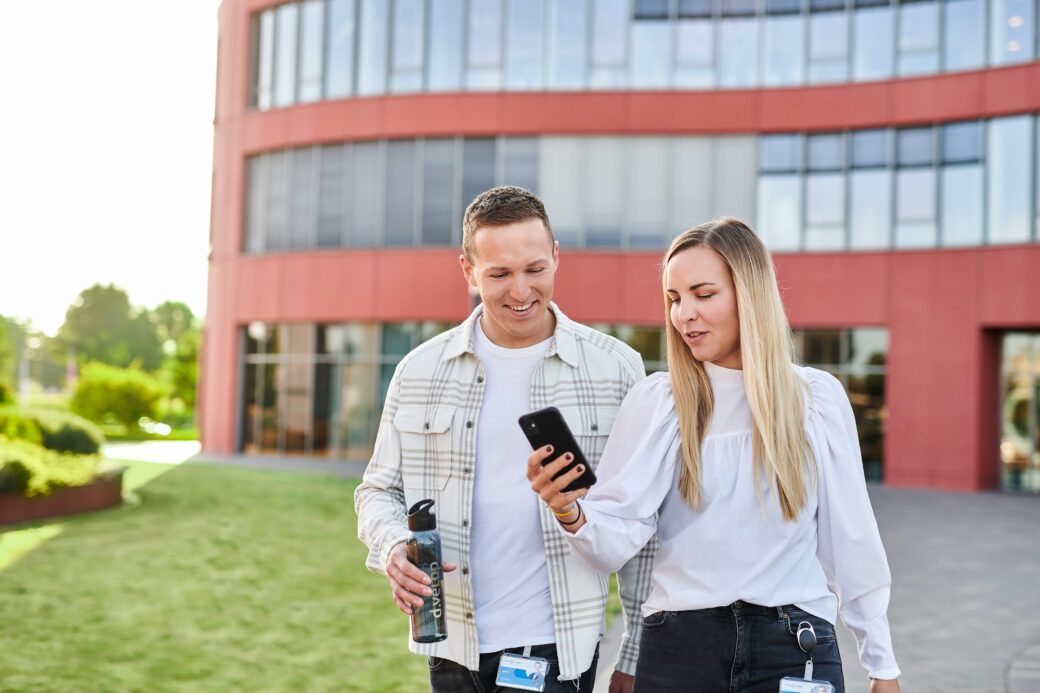
Whitepaper
Digital document management explained
A document management system (DMS) is the first and most important step toward the digital transformation of your company. In our white paper, we show you how a digital document management system can help you make a smooth and easy transition into digitization.
Agenda
- Understanding digital document management
- The difference between ECM and DMS
- The 7 most important functions at a glance
- Step-by-step instructions for introducing a DMS
- Expanding and improving your system
- It’s time to topple analog working from its throne
- Send SIGNals with digital signing
Financially, the d.velop products are also a great benefit for us. After the introduction of the invoice workflow, we were able to increase the cash discount income to 20,000€ already within one year.
Tina Altner
Head of Process Management and Sustainability
GREIWING logistics for you GmbH
Additional d.velop Solutions in Use
In addition to the move to the cloud, GREIWING also opted for further services from d.velop AG – including the digital project file, the digital personnel file, and digital invoice processing. “Moving to the cloud naturally frees up working time,” says Oberfeld, “and with digital invoice processing, we can immediately see when documents haven’t been approved. The finance department can react accordingly. As a result, our cash discount earnings have increased significantly.”
Outlook for digitisation at Greiwing until 2020
“d.velop is one of three pillars of the digitization strategy of GREIWING logistics foru you GmbH,” Matthias Gehrigk describes the partnership-based cooperation between the two companies. So it’s no surprise that many more joint projects are planned for the coming years. In order to further advance digitalization, additional projects are to be realized together by 2020 and existing solutions are to be expanded. Planned are:
- Expansion of the logistic app
- Expansion of digital payroll
- Introduction of additional digital files
- Establishment of a procurement process via SAP
Software Demo
Learn more about the d.velop software
Request your personalised live demo of the d.velop software with just a few clicks. Get a live demonstration of the software and ask your questions directly. Simply fill in the form and we will get back to you.