They occur in every company, regardless of the industry, company size or department: business processes. However, they are not always efficient. Some process steps are even superfluous, time wasters and associated with high operating costs. To prevent this, process modelling is an effective discipline, ensuring that each identified part of the processes is necessary and adds value to the business. By breaking down each process flow step by step, it is possible to identifying and eliminate unnecessary steps and remove bottlenecks. Importantly, specialist departments can now become active in this approach, utilising a flexible tool to modify, enhance and streamline. How? You will find out in this blog article.
Definition of process modelling
Process modelling is the graphic representation of processes and workflows. The visual representation serves to make processes easier to understand, identify inefficiencies and to have the flexibility to resolve.
Questions are answered such as: Where is the beginning and where is the end of a process, or: What is the trigger and which event concludes the process? Are there ambiguities in the responsibilities that are delaying the process? Where can process steps be shortened or even eliminated? It becomes clear that process modelling makes a significant contribution to efficiency and in turn, leads to cost savings, increased productivity and ultimately, enhanced customer satisfaction.
Why process modelling is a must
The aim of process modelling is simply to achieve a representation of a series of steps, triggers and tasks, that make up the process. The graphical representation creates a basis for optimising processes, especially business processes. Everyone involved can review and comment on any specific part of the flow, using their knowledge of the current process to address improvement. Process modelling supports:
- Uncovering inefficient processes: Unnecessary steps, bottlenecks, gaps or assessing the introduction of automation options to enhance flow.
- Save Time and Costs: By eliminating unnecessary steps and automating the remaining steps, can reduce enormous amounts of operational time and subsequently, reduce operating costs.
- Adding automations: Banal activities can be identified, assessed for intelligent machine or software intervention, streamlining processes and reducing process costs. In addition, this can remove the need for human data entry, reducing repetitive processes and eliminating data entry errors hyperautomation.
- Relieving employees: Unnecessary steps are an annoying and demotivating matter, especially for employees. The time could be used for more meaningful activities, which also increases employee satisfaction and motivation.
- Coordinating responsibilities and communication: Responsibilities for individual process steps are made clear and communication between different people or units is simplified.
- Digitise business processes: The digitisation and automation of business processes make every day work life easier. Many routine tasks that were always done by hand can now be done with workflows. Keyword: workflow management.
In the future, specialist departments will model processes themselves
Business departments are the ones who quickly identify inefficient steps and problems, as they are closest to the business process. They know on a day-to-day basis exactly which steps are efficient and which steps require change. If departments had the ability to eliminate inefficient process steps themselves without having to wait for the IT department, overall productivity would be enhanced.
Specialists can now take the first step and independently outline their processes. This reduces the actual development process enormously; fewer communication errors occur and importantly, streamlines beneficial departmental changes.
But how can process optimisation be implemented successfully?
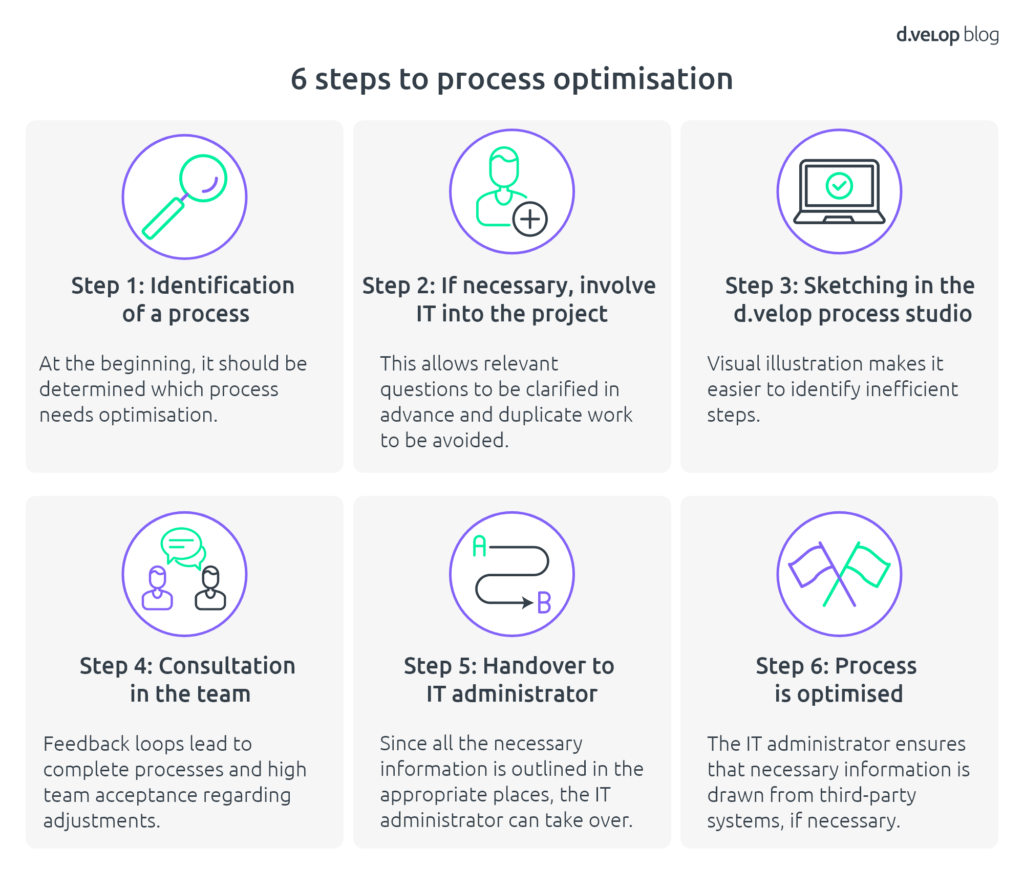
First, it has to be determined which process needs optimisation. If necessary, IT can then be involved in the project. In the third step, the sketching takes place in the d.velop process studio. Inefficient process steps are easier to recognise and the optimisation can be displayed visually. A critical part of the process is to evaluate department knowledge, this gaining different perspectives and opinions, whilst benefiting from increased acceptance by the team. Some processes can be optimised and implemented independently by the specialist departments; other (complex) process optimisations require support from the IT department – this should be decided individually.
Process modelling without IT knowledge – that’s how it works!
With the help of no-/low-code platforms, specialist departments are able to map and automate their processes themselves. With suitable editors, such as the d.velop process studio, processes are outlined using various elements. External systems can be seamlessly integrated and data can be easily included. The following video shows what this can look like using the example of an approval process:
Our conclusion
Process modelling does not have to be the responsibility of the IT department. Specialist departments can take the first step themselves and no longer have to wait for the optimisation of internal processes. Can you think of processes that require optimisation? Then don’t wait any longer and get started with the d.velop process studio!
Demo for the d.velop process studio 💻
Book your individual software demo for the d.velop process studio in our document management system with just a few clicks. Let our experts show you the software live and ask your questions directly.