Customized production involves complex projects with a variety of specialist departments: At the OPTIMA packaging group, digital project files help to store information centrally and in a structured way.
Who is OPTIMA packaging group?
Headquartered in Schwäbisch Hall, Germany, OPTIMA packaging group is a globally minded corporate group that specializes in highly innovative filling and packaging machines. The owner-run company operates in 12 countries and is experiencing dynamic growth. It is a medium-size enterprise with a worldwide workforce of 2500 employees, of whom 1700 work at the Schwäbisch Hall site. OPTIMA packaging group tailors solutions for its customers from various sectors including pharmaceuticals, consumer goods specialists and sanitary paper products through its four business units “OPTIMA pharma”, “OPTIMA consumer”, “OPTIMA nonwovens” and “OPTIMA life science”.
Since these customer projects generally involve custom production as opposed to series production, the projects can run for up to two and a half years. A variety of specialist departments help to carry out the project and a huge number of documents are created, edited and exchanged: from sales agreements to technical specifications such as circuit diagrams, from operating instructions and spare parts lists to machine documentation and acceptance certificates.
Especially the customization creates the necessity for central and structured storing as well as availability of project documents.
Why do they need machine project files?
Project documents were stored on numerous drives in the various folder structures used by the different departments. Consequently, an enormous amount of effort was required to find the relevant documents. There were also irritations when different versions of the same documents were stored multiple times, resulting in duplicated work and preventing the company from ensuring its archiving was audit-proof.
The situation was making everyone involved in the process unhappy. With that in mind, the company decided to make a change for the better and aimed to introduce digital project files for every single “machine project.”
The chart below illustrates its starting position:
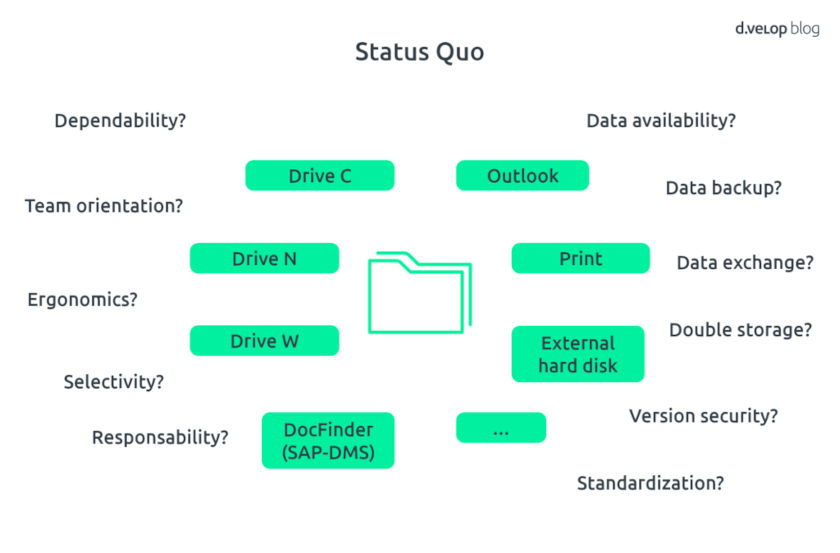
OPTIMA packaging Group hoped to overcome the challenges and issues it faced by rolling out document management software from d.velop AG across the company.
The aim was to gather every single document in the value creation process and make them available in one central, company-wide archive. This massive project was broken down into several sub-projects, including the introduction of digital personnel records, customer files and supplier files.
One of the people responsible for the successful rollout of the machine project was and is application administrator Olga Luk, who has worked for OPTIMA packaging Group since 2009. Together with project manager at d.velop AG Patrick Hörmann, Ms Luk gave a fascinating presentation about the rollout of the digital project folders in the company at the d.velop forum 2019.
Below, we hope to outline the insights gained in and around the rollout of the project folder at OPTIMA.
The process for machine project files at OPTIMA
Until now, the project has focused on significant improvements to the quality and user friendliness of document processes. The intuitive navigation system, more convenient storage features, the implementation of a template management system and simple search functions are intended to make storing, editing and finding the relevant documents much easier.
With a standardized file structure and integration into upstream systems – in the case of OPtIMA to SAP ERP, SAP CRM and SAP Prjects as well as MS Outlook – all project documents can be combined in one digital project folder.
“Working with a digital file structure has to provide added value for the user – it has to be cool to use it” – Ms Luk sums it up in a nutshell discussing the subject of user friendliness in her presentation.
To achieve these ambitious goals in the best possible way, the team defined specific project tasks, including process mapping in d.3ecm, the company-wide consolidation of storage structures and the standardization of document templates.
The scope of the project must be clear
“Before starting the project, we first had to establish an overview of the dimensions of the project environment,” says Olga Luk. One fundamental aspect was to make all staff who were involved and affected familiar with the mindset. “Employees have grown used to certain processes and procedures over the years, which does not make it any easier to introduce new file structures,” says application administrator Olga Luk of past experiences.
Another major aspect is the sheer scope of the machine projects: in one large project, there can be up to 2,000 different documents with all kinds of file types, covering both internal and external correspondence. Nearly every department at OPTIMA has some form of involvement in such a customer project, including sales, project management, project procurement and various specialist technical departments who are responsible for mechanical, electrical or software-related issues. There is also a whole range of employees who are not involved in the digital processes on a daily basis, such as the assembly teams and service technicians.
All these knowledge carriers within the company must be considered as part of “Change Management” to ensure that the project is carried out successfully in this complex project environment. Despite the frequent differences in opinion and perspectives, reports Olga Luk, no one “spoilt the broth.” Instead, the experience and skills of staff enriched and heightened the quality and results of the project.
The first step: forming interdisciplinary project teams
The subproject for digital machine project folders was launched in April 2015 with the formation of the project teams.
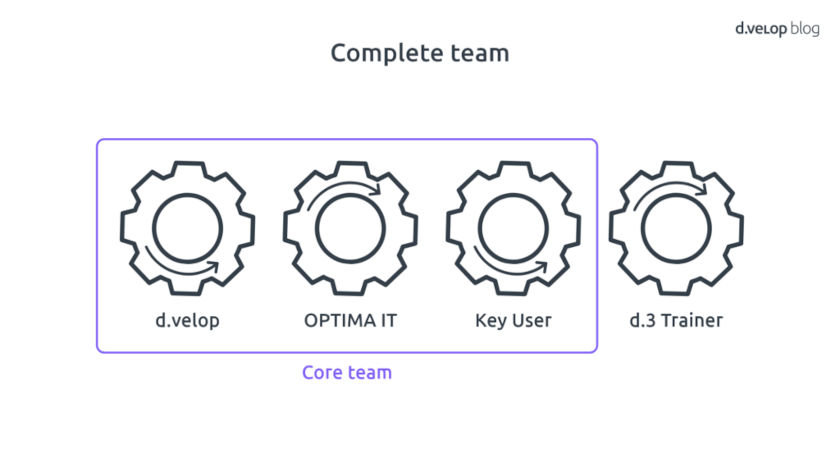
A core interdisciplinary project team with members from all the OPTIMA business units was formed and gradually expanded with additional users from the specialist departments involved as the project progresses.
This team is primarily made up of key users from the sales, project management, technical documentation and engineering departments. The team is supported and moderated by the OPTIMA IT department, which provides IT management, project management, SAP development and user support.
On the part of d.velop AG, the core project team is led by Patrick Hörmann with support from colleagues from the Basis and BPM (Business Process Modeling) environments. The aim of the 20 to 25-strong core team is to design and develop the machine project folders.
The project team is rounded off by specialist users from the technical departments – known as d.3 trainers. With the support of these 25 trainers, the developments are put to the test and approved, and the knowledge is passed on to the company.
“Involving staff from the affected specialist departments helps to get them on board, instead of just delegating new instructions,” explains Ms Luk.
The first workshops focused on the “company-wide consolidation of the storage systems,” while also gathering the opinions and requirements of key users from the business units and the individual departments in relation to the contents and structures of the machine project folders to be created. The aim of this series of workshops was for people to get to know each other, to develop a shared understanding of the situation and ultimately to establish a willingness to compromise between the four business units at OPTIMA.
Prototype development and testing as an essential part of the project
With the development of two software prototypes resulting from these workshops, the focus quickly switched to visualized practice. This enables key users to learn how to work with the systems and not lose themselves in theoretical discussions. Multipliers from the different departments who had not been involved in creating the structures in the workshops were invited to test the prototypes. As independent testers, they simulated the storage and use of project documents from their respective departments.
In the tests, the structure developed for the machine project folders proved itself to be sufficiently intuitive. Once the file structure of the prototype was finalized and additional important functions were added, it was quickly approved for implementation in the first business unit “OPTIMA life science”.
Agile methods in the project rollout
The machine project was successfully and efficiently rolled out in the individual business units based on an agile project method. A fundamental element of this method was maintaining iterative scheduling.
New functions were supplied for the project folder in three-month cycles (versions). Each version consisted of three development sprints and one quality assurance (QA) sprint lasting three weeks. At the end of each sprint (that is, after three weeks), the development results were presented to key users and trainers in the test system as part of a sprint review. This gave users the opportunity to voice their requirements and requests for corrections promptly and regularly so that they could be taken into account in subsequent sprints.
The QA sprint also involved a mandatory guided “Delta Test & Training” event for all key users and trainers. The result was that each QA sprint allowed the developers to put quality-assured, documented and pre-tested functions into production on the one hand, while the training prepared key users and trainers for the new functions on the other, simultaneously supporting the transfer of knowledge within the company.
It was difficult to develop the digital machine project file in one go, so the chosen method of providing an enhanced version of the production system every three months was expedient. It allowed us to continuously improve and supply the product – the digital machine project file. We also did not perform the changeover from decentralized storage to d.velop DMS in all the business units simultaneously. We intended to switch one BU after the other to using the digital folder.
Olga Luk about the benefits of the method
Starting in 2016 with the smallest business unit, OPTIMA life science with around 80 employees, the machine project folder was used in everyday practical work and further optimized for the other units. As well as technical improvements, the team was able to gather many useful experiences of an organizational nature. That made the next productive rollout even more effective and efficient.
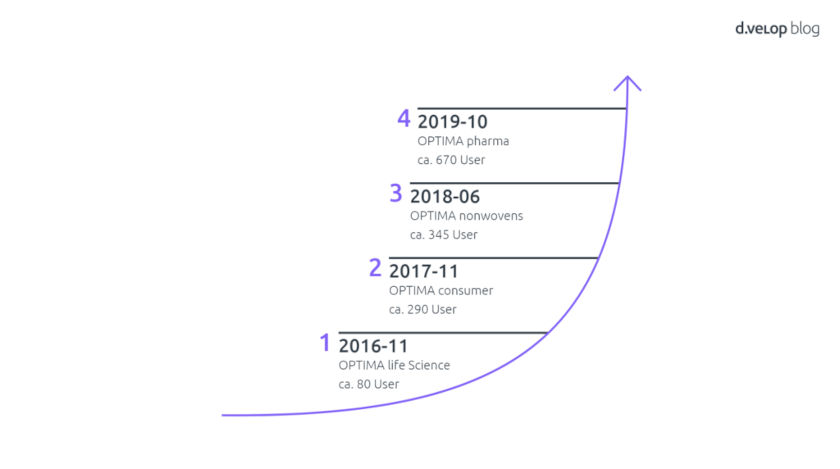
Each business unit appointed its own project leader for its own rollout. This team leader was in charge of communication and organization within that business unit. “A productive rollout is ultimately not a d.velop project and not purely an IT project, but an OPTIMA project; therefore, we needed the backing of our own internal project leaders, our staff,” Olga Luk explains conclusively during her presentation at the d.velop forum 2019.
At what stage are the project files now?
As at June 2019, the productive rollout of the machine project files has been carried out successfully in three of the four business units. Around 850 users now work with the latest version (version 10) of the digital machine project folder.
Version 11, which is the final version, will fulfill the last of the functional requirements and will be rolled out to the last and largest business unit, OPTIMA pharma (and its roughly 630 users) in October 2019.
The machine project files for OPTIMA packaging group are therefore coming to a successful conclusion. Any users that have been asked about what the machine project files rollout has changed during the regular reviews have consistently responded with positives:
- Business units are exchanging information with each other more effectively
- Documents are much easier to find thanks to the simple search function
- The folder is more secure and less redundant than the network drives
- Outlook inbox is now more tidy and clear
- Increase employee autonomy – everyone can look for and store documents easily
- Old versions of documents can be searched for and accessed effortlessly
The list goes on. There was also praise for the excellent project rollout and support from the internal IT department.
Where to now?
We asked the responsible project manager, Ms Olga Luk, what she envisions for the project in the future and what advice she has for other companies in a similar situation:
“At this point, I would like to quote someone myself, and that someone is Christian Lindemann from the d.velop Forum 2019: “[..] companies, [..] products, [..] people.” My interpretation of that actually fills me with optimism, because every user is a human!” No matter the company or the product – if people have to do something that they cannot or do not want to do, they instinctively look for a way around it. And then they land back where they started. In our case, that was the situation with decentralized storage. But when they really want something, what can stop them from achieving the targeted result?”
Advice for project files and change management
“I would advise other companies in the same situation not to underestimate the challenges involved in change management, to see them as something natural and to not quit. Regardless of whether you are a software supplier or an IT department, get yourself into a position where your primary task is to deliver a good system or product. Follow the motto “ordered and delivered.”
Taking on the added effort to integrate users into the project directly and building trust increases added value, because the people represent the project (in the same way as a product or a company). Christian Lindenmann said “People trust people.” If you take away uncertainty and increase people’s confidence in the fact that new questions will be responded to with flexibility, and that support will always be given willingly, you create the space for open and honest communication. And if you communicate closely with your users, you can show your hand and work together to find the right compromise if difficulties or problems arise.
Achieving your goals with d.3 and the d.velop products
Of course, it is not possible to personally include and motivate every end user in a project, but the “trendsetter” principle does not just apply to the fashion business – if you start with a few brave individuals and give them a little confidence, they will carry it on. We have recently been hearing a lot about artificial intelligence and machine learning for improving products and applications. But what about the concept of emotional intelligence? End users (people!) learn information by linking it to an emotion. We were very proud to present the quote from our end users, “We love d.3 [..]” during the presentation, but we never said it was love at first sight. I would therefore give them this advice: if you want it, who can stop you from achieving your goal?”